Roofs:
“New” roof materials are being observed in the Greater Phoenix Metro. While not “new” in the sense that they are a new technology, these materials have been around for some time, they are showing up on some new builds and some remodels. Specifically metal for sloped and rubber for flat roofs are being installed in residential applications primarily because their price points, while high on an absolute basis, are competitive when one looks at a total cost of ownership. 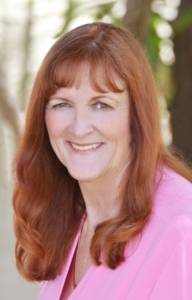
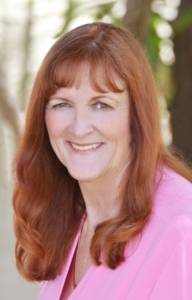
Both these roof materials have very long lives (and respective warranties when installed by experienced and licensed roofers). And in the case of standing seam metal roofs, they provide an updated architectural look. (Most people don’t see flat roofs, unless they are flying a drone, so that benefit is not applicable to the rubber roof application.)
Expect to pay 2X to 3X for these roofs over asphalt type materials or tile type materials, but you can also expect 40-50 year life assuming proper ongoing maintenance.
The downside to these materials is specific durability. While they hold up well to our intense solar load, a metal roof can dent easily from impacts, primarily tree debris, but also hail damage. Rubber roofs do much better in this area, but are susceptible to tear damage, especially if there is mechanical equipment on the roof that needs maintenance or replacement. Extra care must be taken to protect roofs from this type of damage.
While the vast majority of inexpensive roofs are still asphalt materials (either basic shingles or raised profile shingles for sloped roofs and rolled composition for flat roofs), the quality and durability of these roofs have also improved, with the newer architectural shingles (RP) routinely having 25 and 30 year material warranties. Even polyfoam for flat roofs have improved, primarily due to improved seal coats. Regular application of seal coats can extend properly installed foam roofs almost indefinitely.
And having said all that, probably the best value, as in balance between first cost, expected longevity, and durability is still a concrete tile roof with an inorganic underlayment. These can last 30+ years at a reasonable cost and routinely hold up to our infrequent but powerful weather events.
Attic ventilation:
Most attic spaces in Arizona benefit from proper ventilation, both from an energy use standpoint, and also extending the life of roofing materials. There are some attics that do not need to be ventilated, primarily based on the location of the insulation material. Good examples include sloped roofs where the insulation is applied to the underside of the roof deck (i.e. sprayfoam) or any flat roof where the insulation is attached to the underside of the roof deck. If the insulation is anywhere else, the attic should be ventilated.
A good rule of thumb regarding ventilation rates is 1 SF of free area vent for every 300 SF of attic. Further, for every SF of vent space, about 50% should be “high” and 50% “low”. Take a conventional gable roof attic space on an 1800 SF house. The rule of thumb calculates 6 SF of vent. Keep in mind that most vents have baffles to keep water out and screens to keep insects and birds out, so the typical vent has a 50% free area ratio, so the 6 SF of vent is actually 12 SF of vent openings. Next, take the 12 SF and divide it by 2 and you end up with 6 SF of “high” vent and 6 SF of low vent. One could use a ridge vent or gable vent for high vents and a soffit or deck vent for the low vents. Knowing the free area of each vent type allows one to calculate how many vents of each type are needed.
As Property Inspectors, we don’t do the calculations, but we make quick assessments to determine if the installed vents are sufficient and report that accordingly. Of course, this is an oversimplification/rule of thumb…there are many other “rules” that design professionals must use to meet code requirements. For example, if an attic profile is a long rectangle, there may need to be additional vents required in the center area. There is also a focus on “short cycling”, where a high vent is next to another high vent and defeats the purpose of the low vent providing air to evacuate the entire attic volume (think of a soffit and gable vent arrangement (good), but then someone adds a turbine vent 5 feet from the gable vent (bad). In that “bad” case, air enters the gable vent and goes right out the turbine vent (short cycle) and there is insufficient pressure differential to pull air into the soffit vent, resulting in low air flow at the lower portion of the attic, resulting in increasing attic temperatures.
Of course the real problems occur when there should be vents and none are installed, or they are blocked (i.e. by added insulation). We’ve encountered attics that were 165F on a 105F day, where someone blew in 12″ of insulation, but blocked all the soffit vents!
If you ever have any questions about property inspection topics, don’t hesitate to contact us. Thanks, Marty (Martin Lenich, ACI, PE, Chief Inspector at Inspect-It 1st, Greater Phoenix Metro: 602-318-7480 or MartinLenich@InspectIt1st.com
Feel free to call me, everyone knows I answer my phone 602-688-9279.
Have a GREAT day!
Linda